Automated Synthesis of Photovoltaic-Quality Colloidal Quantum Dots Using Separate Nucleation and Growth Stages
Novel, automated, scalable, and reproducible fabrication method for colloid quantum dots
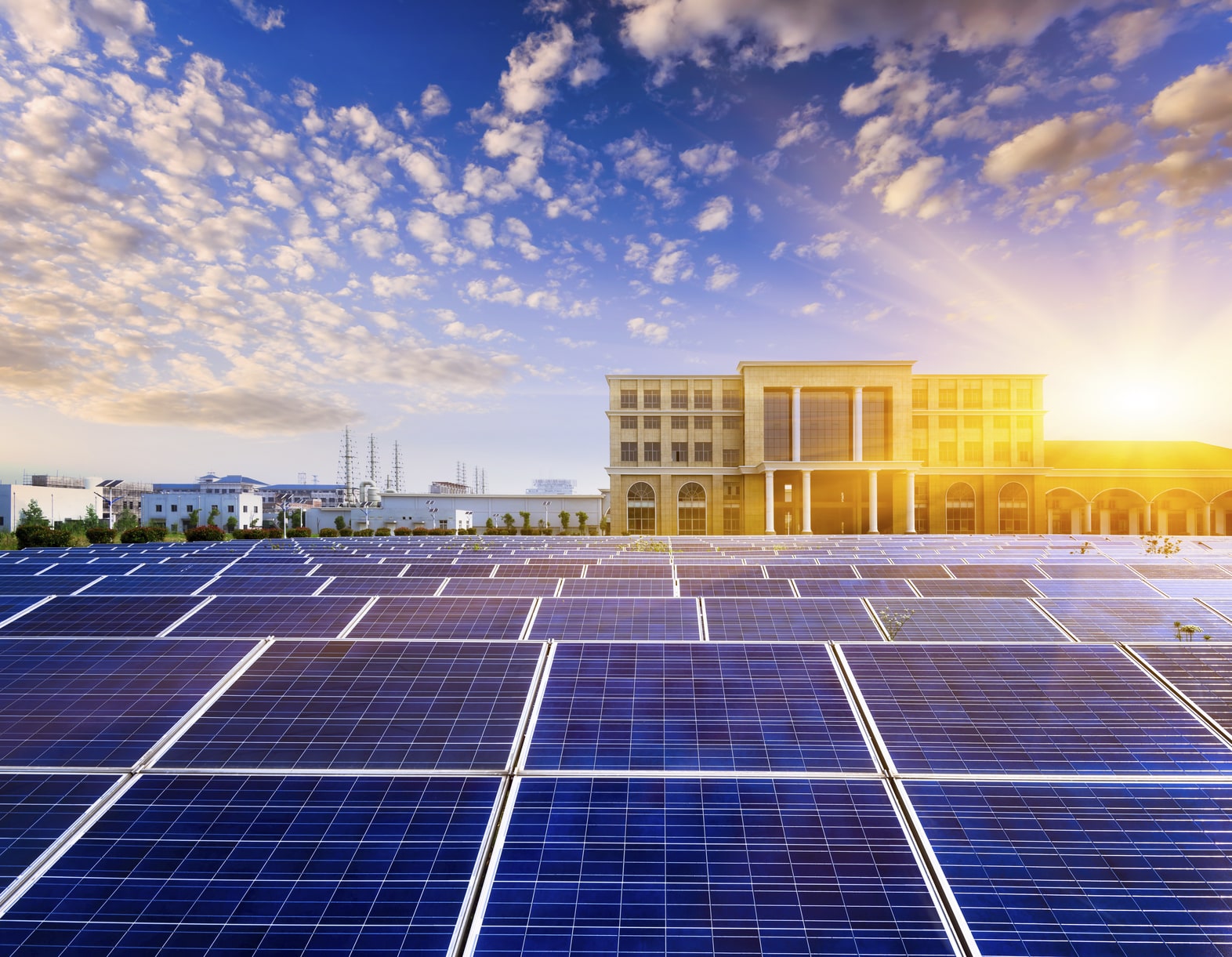
Photovoltaic (PV) cells are one of the most promising renewable energy technologies, owing to their operational feasibility, durability and ease of maintenance. The ever increasing demand for sustainable and renewable energy has resulted in a surge of research on high-efficiency, low-cost photovoltaic systems. The use of colloid quantum dots (CQDs), inorganic semiconductors combining the advantages of organic materials with those of inorganic semiconductors, for solar cells is attractive because they are cheaper than traditional materials and reduce the overall cost of electricity generation. However previous methods of synthesizing CQDs have relied on manual batch processes limiting, the wide use of CQDs in photovoltaics. In order to address this challenge, researchers from KAUST have synthesized CQDs of lead sulfide (PbS) using a novel, automated, scalable in-line synthesis methodology.
Technology Summary
Lead sulfide quantum dots are important semiconductor materials that can be used in solar cells. Three basic components are required for synthesis of lead sulfide quantum dots; a precursor, organic surfactant, and solvent. The synthesis process includes a nucleation and growth period, which is affected by temperature, growth time and precursor concentration. Although the batch fabrication method is effective and mature for producing quality nanocrystals, several challenges still exist: control of the heat and mass transfer, adjustment of reaction chemistries and repeatability of the products.
How It Works
The novel, automated, scalable in-line synthesis methodology for the fabrication of CQDs is based on a dual-stage continuous flow reactor system. The precursor solutions for the system are prepared similarly to a batch synthesis, only deviating by the addition of an inert, immiscible fluid (Fluoroinert FC-70) that aids in maintaining clean reaction channels and keeping a consistent reaction volume and flow rate. The precursors are injected into the system under nitrogen overpressure through micropumps at different points into the mixing stage. The mixed reactants proceed together in a temperature-controlled manner to the nucleation stage. The elevated temperature causes the precursors to react and form nucleation seeds. The purification procedure is similar to the established batch synthesis, involving precipitation of the CQDs using acetone and subsequent re-dispersal in toluene.
Why It Is Better
One of the biggest challenges in the use of CQDs in solar cells is the low power conversion efficiency in the current generation solar cells. Though many attempts have been made to increase the efficiency, the quality of the quantum dots itself is still an essential factor. The developed process enables the fabrication of high quality CQDS with narrowing size distribution in large quantities. The flow of droplets in the fabrication process provides high mixing efficiency, which is essential in particle size control. In addition, higher quality CQDs are produced when there is greater control over the temperature profile in time/space in the flow chamber. Furthermore, separating the nucleation and growth processes provides a greater degree of control to the process, and allows growth to occur at a lower temperature compared to nucleation.
IP Protection
KAUST has a patent pending for this technology.
Invention Track Code
2013-038
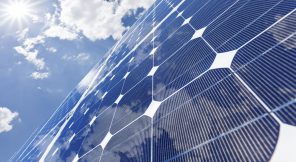
Benefits
- Easily control colloidal quantum dot size distribution with the process producing a narrower size distribution than batch methods, which is essential for quantum dot efficiency
-
Results in improvement in power conversion efficiency
-
Nucleation and growth step are divided by using two different coils, which will be easier for controlling size
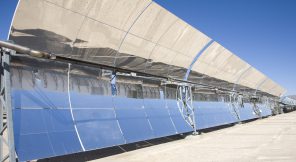
Applications
- Photovoltaics
- Solar cells